Application of Planetary Vacuum Defoaming Mixer in Cosmetics Industry
The planetary vacuum defoaming mixer is a high-efficiency, precision mixing equipment that has been widely applied in the cosmetics industry in recent years. Its unique structure and functions make it an ideal tool for preparing high-demand cosmetic products such as emulsions, creams, serums, and foundations.
1. Main Applications
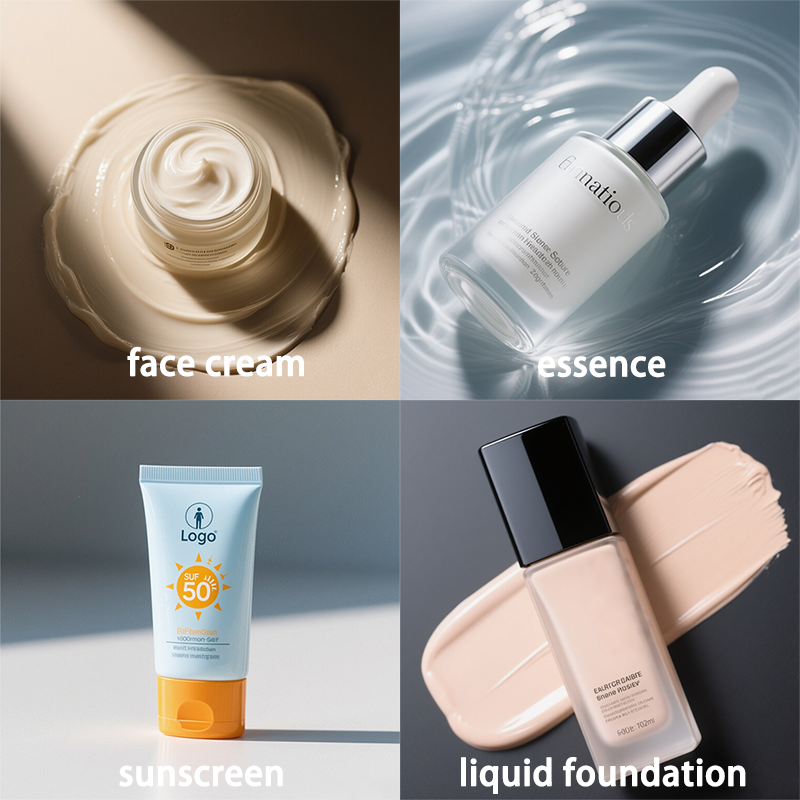
- ◆ Cream/Lotion Preparation: For mixing oil and water phases, ensuring uniform and stable emulsification process, avoiding bubble introduction or separation issues common with traditional mixing.
- ◆ Serum/Gel Products: For high-viscosity or polymer-containing formulations (like hyaluronic acid gels), vacuum defoaming eliminates bubbles, improving product transparency and skin feel.
- ◆ Foundation/Color Cosmetics: When mixing powders with liquid bases, planetary stirring ensures uniform pigment dispersion while vacuum environment prevents powder clumping or oxidation.
- ◆ Mask Slurry Preparation: Quickly removes micro-bubbles from mask liquids, preventing mask sheets from absorbing bubbles that affect active ingredient penetration.
- ◆ Preservative-free/Sensitive Skin Products: Vacuum environment reduces oxygen contact, lowering microbial growth risk and extending product stability.
2. Core Advantages
a. Efficient Defoaming & Homogenization
Vacuum Defoaming: Under negative pressure (typically ≤-0.095MPa), internal bubbles rapidly expand and rupture, solving micro-bubble issues difficult to eliminate with traditional mixing, improving product appearance and texture.
Planetary Motion: The mixer rotates both on its own axis and around the container, achieving three-dimensional dead-angle-free mixing through centrifugal and shear forces, suitable for complex formulations with high viscosity or particles.
b. Paddle-free Design Features
Contamination Prevention: No traditional paddle structure reduces material residue dead angles, lowering cross-contamination risks, complying with cosmetic GMP requirements.
Gentle Processing: Mass transfer occurs through container wall and mixer contact, reducing mechanical damage to heat-sensitive or active ingredients (like peptides, plant extracts).
c. Automation & Controllability
Programmable Parameters: Preset vacuum degree, rotation speed, temperature (some models with heating/cooling jackets), adapting to different formulation process requirements.
Batch Consistency: Precise control of mixing process ensures stability between batches, meeting mass production standards.
d. Wide Material Compatibility
Suitable for oil-based, water-based, silicone-based and other matrices, capable of processing viscosity ranges from low-viscosity serums to high-viscosity creams (up to million-level mPa·s).
3. Solving Industry Pain Points
Comparison Item | Traditional Mixer | Planetary Vacuum Mixer |
---|---|---|
Defoaming Effect | Poor, many residual bubbles | Excellent, bubble residue ≤0.1% |
Mixing Uniformity | Average, with dead angles | Extremely high, 3D dead-angle-free |
Active Ingredient Protection | Prone to shear damage | Gentle processing, good protection |
Production Efficiency | Low, long defoaming time | High, defoaming time reduced by 50% |
- ◆ Traditional Mixing Issues: Traditional paddle mixing easily introduces bubbles, causing product pores, uneven texture or filling difficulties.
- ◆ Low Vacuum Homogenization Efficiency: Ordinary vacuum mixers have long defoaming times, while planetary motion combined with vacuum can reduce defoaming time by 30%-50%.
- ◆ Active Ingredient Protection: Avoids high-speed shear causing ingredient deactivation, suitable for formulations containing easily degradable ingredients (like vitamin C, collagen, etc.).
4. Practical Cases
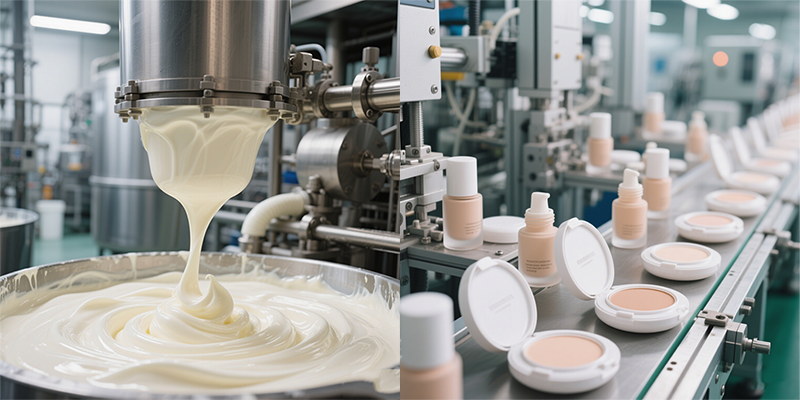
- ◆ High-end Cream Production: After using this equipment, defoaming time was reduced from traditional 1 hour to 20 minutes, cream texture fineness improved, and customer complaints decreased by 60%.
- ◆ Cushion Foundation Development: Mixing powder with liquid base in vacuum environment solved the "mottling" problem caused by powder sedimentation and bubbles.
5. Future Trends
As the cosmetics industry's requirements for product quality and efficacy continue to increase, planetary vacuum defoaming mixers will further develop towards intelligence and modularization, for example:
- ◆ Integrated online quality monitoring (like viscosity, pH sensors)
- ◆ Adaptation to small-batch custom production (like mini models below 10L)
- ◆ Green energy-saving design, reducing energy consumption and carbon emissions
Summary
With its efficient, gentle and controllable mixing and defoaming capabilities, the planetary vacuum defoaming mixer has become key equipment for upgrading production processes in the cosmetics industry, especially suitable for high-end skincare, functional cosmetics and innovative formulation development, helping enterprises enhance product competitiveness and production efficiency.