Application of Planetary Vacuum Defoaming Mixer in Ink and Paint Industry
The planetary vacuum defoaming mixer integrates Bladeless Mixer and Centrifuge Mixer technologies to systematically solve core pain points in the ink and paint industry, including uneven dispersion, bubble residue, low efficiency, and environmental compliance issues.
1. Core Pain Points in Ink/Paint Industry
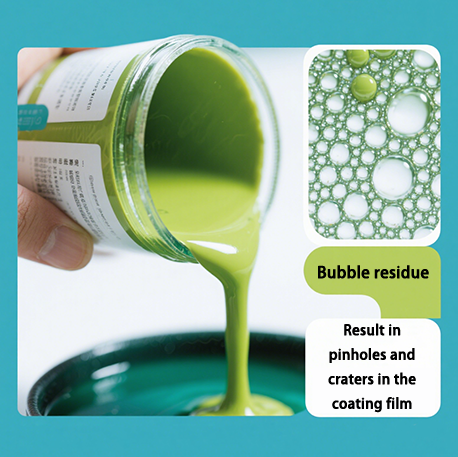
Dispersion Challenges
- Nano pigments/fillers prone to agglomeration: Such as carbon black and titanium dioxide, causing color difference, uneven gloss or reduced conductivity (conductive ink resistance fluctuation >10%).
- Dead zones in high viscosity systems: For example, thixotropic epoxy paint with traditional stirring has dispersion fineness >20 μm, affecting coating adhesion (ASTM D4541 test peel strength <5 MPa).
Bubble Residue
Solvent volatilization or mechanical stirring introduces microbubbles (10~100 μm in diameter), causing coating pinholes, shrinkage cavities or printing line breaks, with rework rates as high as 8%~15%.
Efficiency and Environmental Protection
Traditional processes require step-by-step mixing and defoaming, with long production cycles (>6 hours per batch) and excessive VOC emissions (e.g. toluene concentration >50 ppm).
2. Technological Breakthroughs of Planetary Vacuum Defoaming Mixer
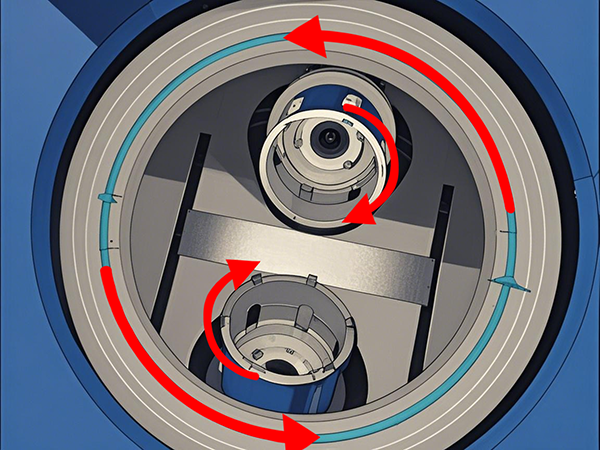
1. Integrated Bladeless Mixer Technology: Blade-free High Shear Dispersion
Principle: The planetary gear system drives the container to rotate (1~50 rpm) and the stirring paddle to rotate (50~150 rpm), forming a three-dimensional spiral flow field to replace the linear shear of traditional paddles.
Advantages:
- Zero dead angle mixing: The blade-free structure prevents high-viscosity materials (such as 500,000 cps UV glue) from accumulating on the tank wall, improving dispersion uniformity to 99.5% (laser particle size analyzer detects D90≤5 μm).
- Low shear damage: Bladeless design reduces breakage of brittle materials (such as glass beads and cellulose fibers), maintaining the integrity of functional fillers.
2. Integrated Centrifuge Mixer Technology: Centrifugal Force Enhanced Dispersion
Principle: In a vacuum environment, centrifugal force (acceleration up to 2~5G) is used to throw materials toward the tank wall to achieve dynamic layering and remixing.
Advantages:
- Nano-level dispersion: Centrifugal force overcomes van der Waals forces, enabling stable suspension of nanoparticles (such as graphene and quantum dots), with conductive ink resistivity fluctuation <2%.
- Efficient defoaming: Bubbles gather toward the axis under centrifugal force, combined with vacuum suction (vacuum degree ≤-0.095 MPa), reducing defoaming time to 30 minutes (traditional static defoaming requires 4~8 hours).
3. Vacuum-Temperature Control Synergistic Process
- Precise defoaming: The vacuum system enables adjustable gradient defoaming (e.g. stepwise pressure reduction to -0.08 MPa→-0.1 MPa), avoiding surface skinning of high-viscosity materials.
- Temperature control: Jacket heating/cooling (temperature control accuracy ±1°C), suitable for low-temperature solvent-based coatings (such as -10°C chlorinated rubber paint) or high-temperature reaction systems (such as 80°C epoxy curing).
3. Performance Comparison with Traditional Equipment
Indicator | Planetary Vacuum Defoamer | Traditional Centrifugal Mixer | High Speed Disperser |
---|---|---|---|
Dispersion Fineness (D90) | ≤5 μm | 10~20 μm | 15~30 μm |
Bubble Residue Rate | <0.05% | 0.3%~0.8% | 0.5%~1.2% |
Applicable Viscosity Range | 1~500,000 cps | 1~100,000 cps | 1~50,000 cps |
Energy Consumption (kW·h/ton) | 18~25 | 30~40 | 35~50 |
4. Industry Application Cases
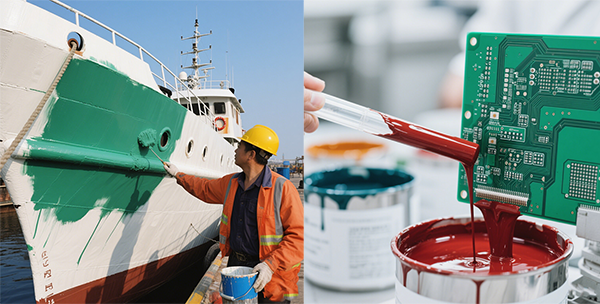
Case 1: A PCB Ink Manufacturer
Pain point: Uneven resistance of silver conductive ink (fluctuation ±12%), causing circuit impedance to exceed standards.
Solution: Using planetary vacuum defoamer, Bladeless Mixer achieves silver powder dispersion D50=1.2 μm, resistance fluctuation <±2%, reducing customer complaint rate by 90%.
Case 2: Ship Anticorrosive Coating Upgrade
Pain point: Zinc powder sedimentation after traditional stirring, coating salt spray test only 500 hours.
Result: Centrifugal force mixing ensures uniform zinc powder distribution, improving salt spray corrosion resistance to 2000 hours (ISO 9227 standard).
5. Future Technology Integration Directions
- AI process optimization: Real-time feedback of material viscosity through torque sensors to automatically adjust speed and vacuum degree.
- Modular design: Replaceable Bladeless paddles and Centrifuge modules to adapt to multi-category production.
- Zero carbon emission process: Integrated heat pump recovers waste heat from vacuum system, reducing energy consumption by 15%~20%.
Summary
The planetary vacuum defoaming mixer provides an integrated solution of high-precision dispersion, deep defoaming and green production for the ink/paint industry. Its digitally verified performance improvements and cost savings in real cases make it an indispensable core equipment for industry upgrading.